Four-link (Semi-Hotchkiss) Drive
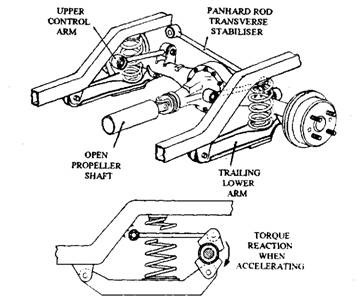
Four-link (Semi-Hotchkiss) Drive When helical springs are used in conjunction with a live rear axle, these springs cannot take driving and braking thrust, torque reaction or give lateral support to the rear axle. Therefore additional arrangements must be incorporated to meet these requirements. It may appear that the helical spring provides a reduction in the unsprung weight, but in practice when the weight of the additional locating arms and rods fitted to support this arrangement is added, the unsprung weight difference becomes very small. However, this layout allows for an accurate positioning of the axle which is an advantage. The rear axles is positioned by upper and lower trailing suspension arms in the four-link drive system layout as illustrated in Fig. 26.29. These arms transmit driving thrust and prevent rotation of the axle casing. A transverse stabilizer, called a Panhard rod, connects the rear axle to the vehicle body and thereby controls sideways movement of the axle.