Control Valve Principle
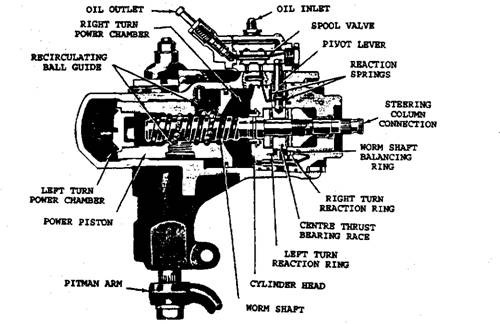
Control Valve Principle Types and Operation During operation of the engine, the fluid in power steering keeps flowing from the pump to the control valve, then back to the reservoir and both the pressure surfaces are exposed to the same system pressure. In the straight ahead position of the wheel, the fluid flows through the circuit. With the increase of steering effort, the valve shift also increases exerting proportional amount of pressure by directing fluid to one pressure surface and increasing the size of the return passage opening from the opposite pressure surface to the reservoir. Figure 27.66 illustrates the principle of operation of the control valve in neutral and during a turn. The control valve is either located inside or is attached to the exterior of the integral type power steering gear. In the link type power steering gear, the valve may be built into the end of the power cylinder or be a separate unit. The mechanical input force applied by the steering wheel on one han